Bajaj Bs-6 three wheeler taxi Clutch comp.
Pictures of details
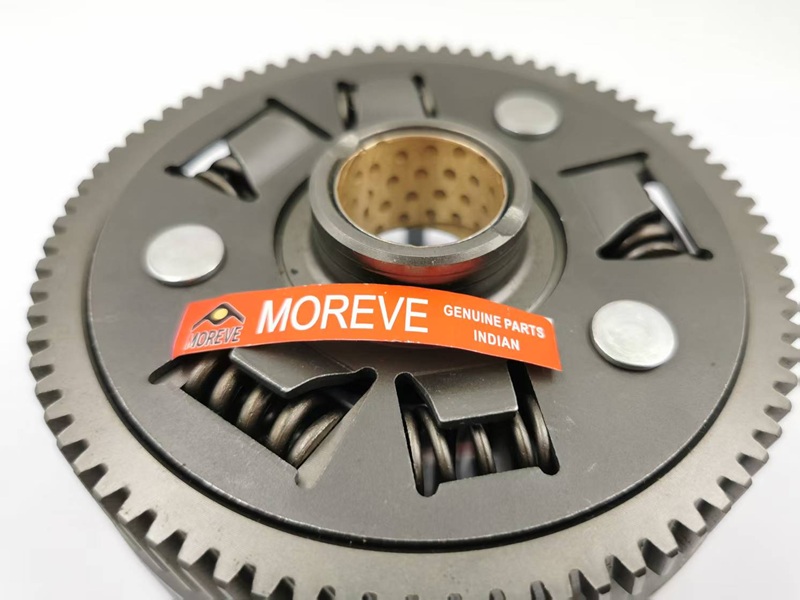
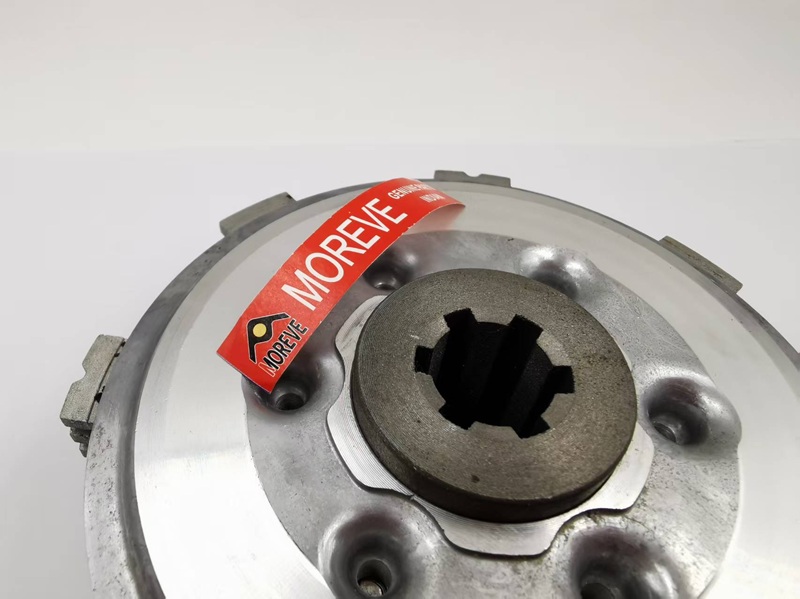
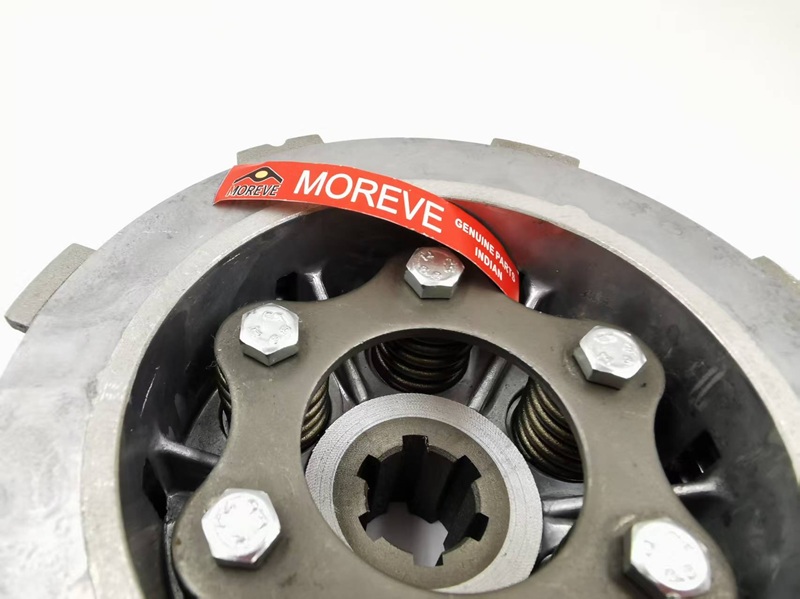
The core components of the clutch assembly
The core components of the clutch assembly include the following key parts, each of which plays a vital role in the performance and function of the clutch:
1. Pressure Plate
Function: The pressure plate presses the friction plate to the flywheel through the pressure of the spring or diaphragm spring to transmit the power of the engine.
Material: Usually made of high-strength cast iron or steel, and the surface is heat-treated to improve wear resistance.
2. Friction Plate
Function: The friction plate is located between the pressure plate and the flywheel and transmits power through friction. It has buffering and shock-absorbing functions to reduce the impact in power transmission.
Material: Both sides of the friction plate are covered with materials with high friction coefficients, such as ceramics or organic composites, and there is usually a shock-absorbing spring in the middle.
3. Flywheel
Function: The flywheel is connected to the engine crankshaft, provides inertia to smooth the engine's speed fluctuations, and contacts the friction plate to transmit power.
Material: Usually made of cast iron or steel, and the surface is precisely machined to ensure flatness and friction performance.
4. Diaphragm Spring
Function: The diaphragm spring provides the pressure required for the pressure plate to ensure that the friction plate is in close contact with the flywheel. When the clutch pedal is pressed, the diaphragm spring releases the pressure to separate the friction plate from the flywheel.
Material: Usually made of high-elastic steel and heat-treated to improve durability.
5. Release Bearing
Function: When the clutch pedal is pressed, the release bearing pushes the diaphragm spring to separate the pressure plate from the friction plate and interrupt the power transmission.
Material: Usually made of high-strength steel or ceramic, with high wear resistance and heat resistance.
6. Clutch Cover
Function: The clutch cover fixes the pressure plate and diaphragm spring to protect the internal components from external contamination and damage.
Material: Usually stamped from steel plate, with high strength and heat resistance.
7. Cushion Springs
Function: Cushion springs are located inside the friction plate to absorb and buffer the torque fluctuations of the engine and reduce the impact and vibration of the transmission system.
Material: Usually made of high elastic steel.
8. Spline Hub
Function: The spline hub connects the friction plate and the transmission input shaft to ensure the synchronization and stability of power transmission.
Material: Usually made of high-strength steel, with hardened surface for improved wear resistance.
9. Clutch Pedal and Linkage
Function: The clutch pedal and linkage system transmits the driver's pedaling force to the release bearing to control the engagement and disengagement of the clutch.
Material: Usually made of steel or aluminum alloy, with high strength and lightweight characteristics.
10. Adjustment Mechanism
Function: The adjustment mechanism is used to adjust the free travel of the clutch pedal to ensure smooth and accurate clutch operation.
Material: Usually made of steel or plastic, with high durability and easy adjustability.
These core components work together to ensure that the clutch assembly can efficiently and reliably transmit and interrupt the engine's power while providing a smooth driving experience. The material selection, manufacturing process and quality control of each component have a significant impact on the performance and life of the clutch assembly.
The assembly process and control of the clutch assembly
The assembly process and control of the clutch assembly is the key link to ensure the performance and quality of the clutch. The following are the detailed assembly process and quality control points:
1. Clutch assembly process
1. Diaphragm spring clutch assembly process
Assembly of pressure plate and cover assembly:
Install the elastic cylindrical pin to ensure that the connection between the pressure plate and the clutch cover is firm.
Place the diaphragm spring on the pressure plate to ensure that the spring is in the correct position.
Put the support ring into the bottom groove of the inner cavity of the clutch cover to ensure that the support ring and the cover fit tightly.
Place the assembled clutch cover gently on the pressure plate, and put a gasket between the transmission plate and the clutch cover wall, insert the limit screw and tighten it.
Disconnect finger end jump detection:
Detect the disconnect finger end jump to ensure that the length of the disconnect finger is consistent.
Install the disconnect pull ring assembly, and note that the bulge of the elastic lock ring should correspond to the short finger part.
Comprehensive performance test:
Perform a comprehensive performance test of the clutch assembly to ensure that all indicators meet the requirements.
Insert the retaining ring in sequence to ensure the stability of the clutch assembly.
Dynamic balancing and deweighting:
Dynamic balancing test of the clutch assembly, and deweighting treatment if necessary to ensure the balance of the assembly.
2. Coil spring clutch assembly process
Weighing of release lever:
Weigh the release lever to ensure that the weight of each lever is consistent to avoid imbalance.
Assembly of pressure plate and cover assembly:
Assemble the pressure plate and clutch cover to ensure that the positions of each component are correct.
Adjust the pressure plate and cover assembly to ensure that the dimensions meet the design requirements.
Balancing of clutch cover assembly:
Balancing test of the clutch cover assembly, and drilling and deweighting if necessary to ensure the dynamic balance of the assembly.
Performance test:
Perform performance test of the assembly using a clutch tester to ensure that it meets the factory standards.
2. Key points of quality control
1. Dimensional accuracy control
Use precision equipment such as a three-coordinate measuring instrument to detect the dimensions of key components to ensure the dimensional accuracy of components such as the pressure plate, diaphragm spring, and release finger.
2. Material performance testing
Perform performance tests on key materials such as friction plates and diaphragm springs to ensure that their heat resistance, wear resistance and strength meet the requirements.
3. Assembly process control
During the assembly process, strictly follow the process requirements to avoid imbalance or performance degradation caused by improper assembly.
4. Comprehensive performance test
Perform comprehensive performance tests on the assembled clutch assembly, including separation finger tip jump detection, dynamic balance detection and clutch test machine test to ensure the stability of the assembly performance.
5. Pre-shipment inspection
Before leaving the factory, the clutch assembly is strictly inspected to ensure that all indicators are qualified, and the assembly is marked and packaged to prevent damage during transportation.
III. Precautions
No unauthorized disassembly and assembly: The clutch assembly has been strictly dynamic balanced and performance tested before leaving the factory. Unauthorized disassembly and assembly may cause excessive imbalance and affect the performance.
Avoid contamination of the friction surface: During the assembly process, it is strictly forbidden to contaminate the friction surface with grease, otherwise it will cause the clutch to slip or performance degradation.
Regular maintenance and inspection: During use, regularly check the wear of the clutch and replace the worn parts in time to ensure its long-term stable operation.
Through the above process and quality control measures, the performance of the clutch assembly can be ensured to be stable and the service life is long, meeting the requirements of the automobile transmission system.
Bajaj Re Common Clutch failure and solution
1. Clutch slipping
Fault phenomenon
The vehicle is difficult to start, especially under heavy load.
The engine speed increases, but the vehicle speed does not increase accordingly.
The power is insufficient when going uphill, and even the clutch smokes or burns.
Fault cause and solution
Friction plate wear: The friction plate is excessively worn or the rivets are exposed, resulting in insufficient friction. The friction plate needs to be replaced.
Friction spring failure: The spring elasticity is weakened or broken, resulting in insufficient pressure on the pressure plate. The spring needs to be replaced.
Oil on the surface of the friction plate: Oil causes the friction to decrease. The clutch needs to be disassembled and the friction plate and driven plate need to be cleaned with gasoline.
Improper clutch adjustment: The free travel is too small or the separation lever is not in the same plane. It needs to be adjusted to the specified range.
2. Incomplete clutch separation
Fault phenomenon
It is difficult to shift gears, and even the gears may be knocked.
After the clutch pedal is pressed to the bottom, the power cannot be completely cut off, and the vehicle cannot stop.
Causes and solutions
The clearance between the release claw and the release bearing is too large: the clearance needs to be adjusted to 0.3-0.5 mm.
The free travel of the clutch pedal is too large: it needs to be adjusted to 20-40 mm.
The driven disc is warped or rusted: the driven disc needs to be corrected or replaced.
The clutch shaft spline is worn: it needs to be repaired or replaced with a new part.
3. Abnormal clutch noise
Fault phenomenon
The clutch makes a "rustling" or "clicking" sound when it is engaged or disengaged.
Abnormal noise when starting or shifting.
Causes and solutions
The release bearing is short of oil or damaged: lubricating oil needs to be added or the bearing needs to be replaced.
The friction plate is dirty or hardened: the friction plate needs to be cleaned or replaced.
The driven disc is twisted or the shock absorber spring is broken: the driven disc needs to be repaired or replaced.
The release lever is not in the same plane: the height needs to be adjusted to be consistent.
4. Clutch shaking
Fault phenomenon
The vehicle has continuous impact or vibration when starting.
Fault cause and solution
The pressure plate spring has uneven elastic force or is broken: the spring needs to be checked and replaced .
The friction plate rivet is loose: the friction plate needs to be re-riveted or replaced .
The driven disc hub spline is worn: the driven disc needs to be replaced .
5. The clutch pedal is too heavy or too soft
Fault phenomenon
The pedal feels too heavy or too soft when pressed, affecting the operation .
Fault cause and solution
The hydraulic system is short of oil or leaking: the oil level needs to be checked and the leak needs to be repaired .
Power system failure: the pneumatic cylinder, seal ring and control valve need to be checked .
The clearance between the release bearing and the release rod is too large: the clearance needs to be adjusted .
Material selection and process requirements of the clutch gear
The clutch gear is an important component in the clutch assembly. Its material and process requirements directly affect the performance, life and reliability of the clutch. The following is a detailed description of the material selection and process requirements of the clutch gear:
1. Material selection
The clutch gear usually needs to have high strength, wear resistance, impact resistance and good processing performance. Commonly used materials include:
(1) Alloy steel
Common grades: 20CrMnTi, 20CrMo, 40Cr, etc.
Features:
High strength, high toughness, suitable for bearing large loads.
Good hardenability and wear resistance.
The surface hardness and core toughness can be improved by heat treatment.
(2) Carburizing steel
Common grades: 20CrMnTi, 20CrNiMo, etc.
Features:
The surface hardness is high after carburizing and the wear resistance is good.
The core maintains high toughness and excellent impact resistance.
Applicable to high load and high speed conditions.
(3) Quenched and tempered steel
Common grades: 45 steel, 40Cr, etc.
Features:
After quenching and tempering treatment, the comprehensive mechanical properties are good.
Low cost, suitable for medium load conditions.
2. Process requirements
The processing technology of the clutch gear needs to ensure its dimensional accuracy, surface quality and mechanical properties. The following are the main process requirements:
(1) Forging
Purpose: Improve the internal structure of the material and improve strength and toughness.
Process requirements:
Use die forging or free forging process to ensure that the shape of the gear blank is close to the finished product.
Control the forging temperature and deformation to avoid internal defects (such as cracks and pores).
(2) Heat treatment
Purpose: Improve the hardness, wear resistance and fatigue resistance of the gear.
Process requirements:
Carburizing and quenching: Applicable to carburizing steel, the surface hardness reaches HRC58-62, and the core hardness is HRC30-45.
Quenching and tempering: Applicable to quenched and tempered steel, the hardness reaches HRC25-35.
Tempering: eliminate quenching stress and improve toughness.
(3) Machining
Turning: process the outer circle, end face and inner hole of the gear to ensure dimensional accuracy and surface finish.
Gear hobbing/gear shaping: process the gear tooth shape to ensure that the pitch, tooth direction and tooth shape errors meet the requirements.
The tooth surface roughness is controlled below Ra1.6.
The tooth shape error and tooth direction error meet the GB/T10095 standard.
Gear grinding (high-precision gears): further improve the tooth surface accuracy and finish.
(4) Surface treatment
Purpose: improve the wear resistance, corrosion resistance and fatigue strength of the gear.
Common methods:
Carburizing/nitriding: improve surface hardness and wear resistance.
Shot peening: improve the fatigue resistance of the tooth surface.
Phosphating/plating: improve corrosion resistance.
(5) Inspection and correction
Dimension inspection: Use tools such as gear measuring instruments and three-dimensional measuring instruments to detect parameters such as pitch, tooth shape, and tooth direction.
Hardness inspection: Use a hardness tester to detect surface and core hardness.
Dynamic balance test: Perform dynamic balance correction on the gear to ensure no vibration during high-speed operation.
3. Common problems and improvement measures
Tooth surface wear: Optimize heat treatment process to improve surface hardness; strengthen lubrication management.
Root fracture: Improve material selection and heat treatment process to improve core toughness.
Excessive noise: Improve gear processing accuracy to ensure smooth meshing.
why morever bajaj Re clutch quality is top
Clutch machining process control is a key link to ensure the quality and performance of the clutch assembly. The clutch assembly is usually composed of components such as a pressure plate, friction plate, driven plate, release bearing, etc., and its machining process involves multiple processes and precision control. The following are the main control points of the clutch machining process:
1. Material selection and quality control
Friction plate material: Select wear-resistant, high-temperature resistant materials with stable friction coefficient (such as asbestos-based, ceramic-based or organic materials).
Pressure plate and driven plate materials: Usually high-strength cast iron or steel is used, and the material hardness, strength and heat resistance must meet the requirements.
Material inspection: Chemical composition analysis, hardness test and metallographic structure inspection of raw materials are carried out to ensure that the material performance meets the standards.
2. Processing technology control
(1) Pressure plate machining
Turning: Ensure the surface flatness and dimensional accuracy of the pressure plate, and the roughness is controlled below Ra1.6.
Heat treatment: Quench and temper the pressure plate to improve hardness and wear resistance.
Dynamic balancing test: Perform dynamic balancing on the pressure plate to avoid vibration during high-speed rotation.
(2) Friction plate processing
Molding process: Use hot pressing molding process to ensure uniform thickness and density of the friction plate.
Surface treatment: Slot or punch holes on the surface of the friction plate to improve heat dissipation and friction stability.
Riveting process: When riveting the friction plate to the driven plate, ensure that the rivets are firm and evenly distributed.
(3) Driven plate processing
Spline processing: Ensure the spline size accuracy and surface finish to avoid poor fit with the clutch shaft.
Shock absorber spring installation: Ensure uniform spring preload to avoid torsional vibration.
Dynamic balancing test: Perform dynamic balancing on the driven plate to ensure smooth operation.
(4) Split bearing processing
Bearing accuracy: Ensure the size accuracy and surface finish of the inner and outer rings of the bearing.
Lubrication treatment: Fill the bearing with grease to ensure smooth operation.
3. Assembly process control
Cleanliness control: Clean all parts before assembly to prevent impurities from entering.
Assembly sequence: Assemble in strict accordance with process requirements to ensure that all parts fit well.
Clearance adjustment: Adjust the clearance between the release bearing and the pressure plate to ensure that the clutch is completely separated.
Preload control: Test the preload of the pressure plate spring to ensure uniform pressure.
4. Inspection and testing
(1) Dimension inspection
Use tools such as a three-coordinate measuring instrument and a micrometer to check whether the key dimensions meet the requirements of the drawing.
Check the thickness of the friction plate, the flatness of the pressure plate, the spline clearance, etc.
(2) Performance test
Friction performance test: Test the friction coefficient and wear resistance of the friction plate.
Separation performance test: Test whether the clutch is completely separated and whether the pedal force is moderate.
Durability test: Simulate actual working conditions to test the service life of the clutch.
(3) Dynamic balance test
Dynamically balance rotating parts such as the pressure plate and driven plate to ensure no vibration during high-speed operation.
5. Process Recording and Traceability
Process parameter recording: record the processing parameters of each process (such as temperature, pressure, speed, etc.).
Quality traceability: number each batch of products and establish quality files to facilitate problem tracing.
6. Common problems and improvement measures
Uneven wear of friction plate: optimize the hot pressing process to ensure uniform density of friction plate.
Pressure plate deformation: strengthen heat treatment process control to avoid deformation caused by residual stress.
Incomplete separation: optimize the clearance adjustment process between the release bearing and the pressure plate.
Distributor comments
Our Warehouse and Office